The problem with this technology is that bladders can’t be perfectly precise and very often form wrinkles and creases (much as a tube does when it’s not properly fitted inside a bicycle tire) that result in imperfections and uneven thickness in the prepreg layers, which weaken the resulting frame. Sometimes these bladders are even left inside the frame.
Even the removable forms some bike companies say they use inside the bladders or the use of vacuum bags to evacuate excess air from the mold can’t improve bladder molding enough to make it viable for top-quality bicycle frames. At least one major bicycle manufacturer even acknowledges wrinkles in the exterior surface of some of its bike frames, blaming it on the vagaries of unidirectional carbon fiber. They even ask their customers to think of these defects as unique marks of a handcrafted bicycle. Nonsense: They’re caused by inferior molding techniques.
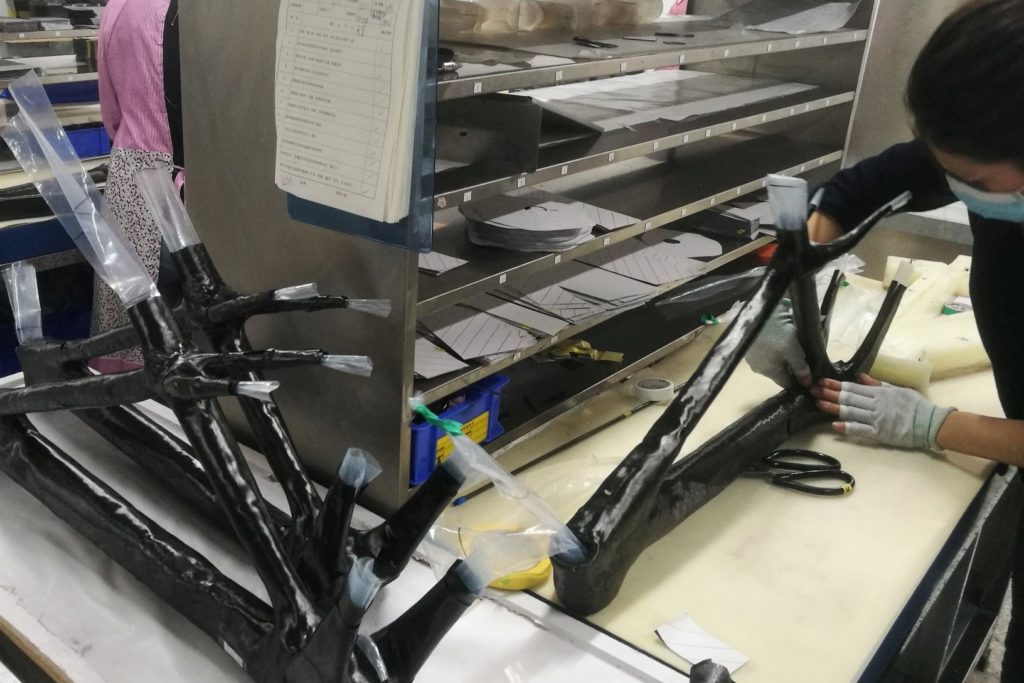
EPS Molding: The State of the Art
Expanded Polystyrene (EPS) molding is the current state of the art when it comes to molding carbon-fiber composite. In EPS molding, a polystyrene inner form is made to the exact shape of the frame and the prepreg layup is done over this. The polystyrene used in EPS molding is very much like the liners of cycling helmets. Under heat it forcibly tries to expand to 40 times its size, completely and perfectly conforming the layers of prepreg to the exact shapes and contours of the outer clamshell mold. After curing, the spent forms are exhausted from the frame by means of high air pressure.
The result is a product with tighter compaction using less material, which means a stronger and lighter frame. It also means a frame with consistent thickness and without any of the imperfections and inconsistencies that bladder molding can leave. These irregularities can lead to delamination and/or premature stress fractures over time. Every fold and every wrinkle are potential points of failure. With EPS molding, the interior of the frame is as smooth and wrinkle-free as the exterior.
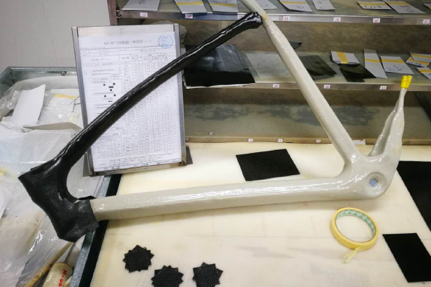
The result is a product with tighter compaction using less material, which means a stronger and lighter frame.
Some frame manufacturers say they use EPS molding only in “critical areas” of the front triangle and some manufacturers avoid discussing it at all, due to the high costs of converting over from bladder molding. Gerard Cycles employs full EPS molding as the key ingredient in our G-Spec CarbonProcess, which ensures the very highest strength-to-weight ratio and an extremely reliable frame.
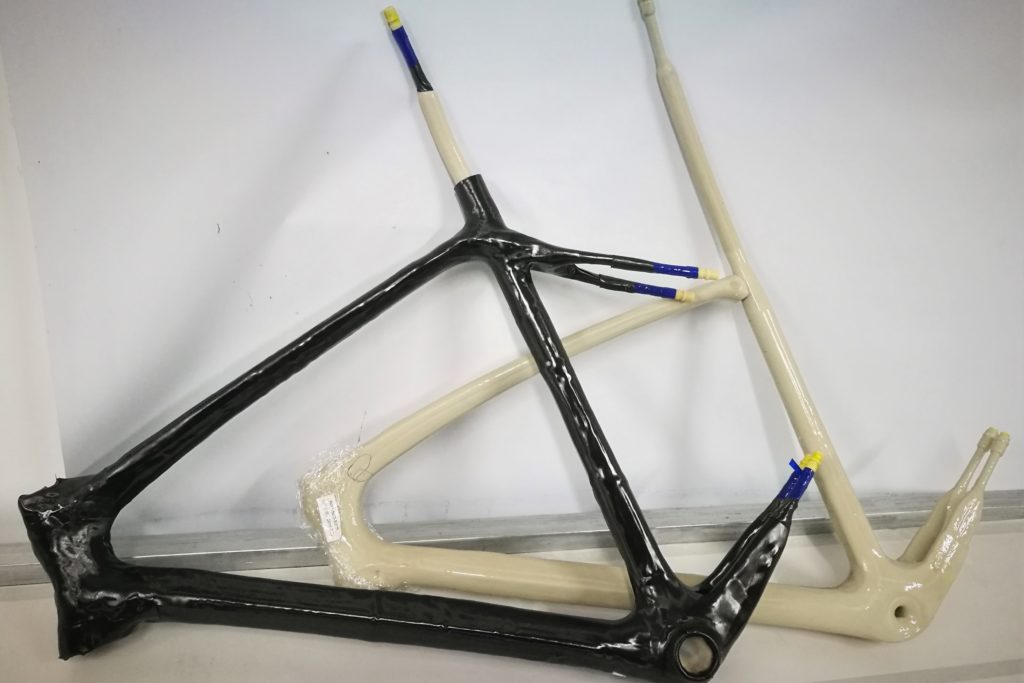
Precise temperature and timing ensure that all frames are uniformly cured in large, industrial ovens. A cured frame straight from the mold shows excess epoxy resin extracted due to the superior compaction of EPS molding. This is a key reason why our frames have such a high strength-to-weight ratio and perform so well.
Monocoque Means a Better Frame
The word monocoque comes from the French, meaning “single shell.” Essentially, it’s a method of constructing a bicycle frame in one piece so that the continuous shell handles stresses and forces as a single unit. This contrasts with older methods, such as “lug and tube” construction (first employed with steel frames) where carbon-fiber composite tubes are glued to lugs (socket-like brackets) to build a frame. This was the method used with the pioneering Giant Cadex 980 C John first raced in 1987.
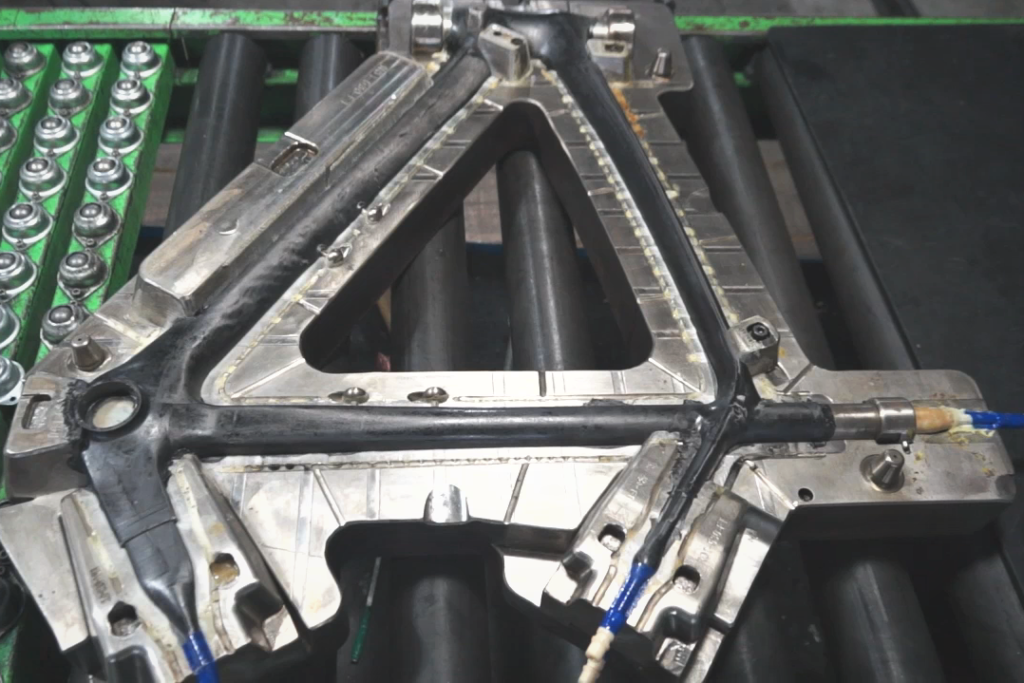
Gerard Cycles constructs its frames with a monocoque front triangle that’s joined with precisely aligned and bonded seat stay—chain stay assemblies, the method used with virtually all high-end bike frames.
The Payoff From G-Spec CarbonProcess
While our state-of-the-art production methods yield lighter frames (the 54cm size Force 100 frame weighs in at under 850 grams), we’re not obsessed with making the lightest frames possible. We’re much more interested in producing frames that are stiff enough and strong enough to deliver the highest performance possible under all conditions. That’s the bottom-line payoff from G-Spec CarbonProcess.
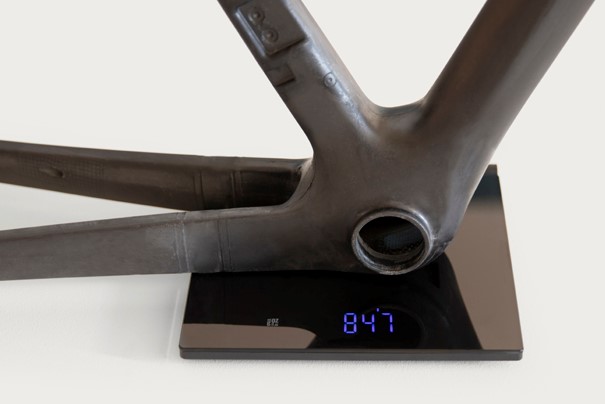
Giant® Cadex 980 C
Giant’s first entry into carbon-fiber bike frames was the Cadex 980 C, first introduced in 1987. A hybrid construction, it featured eight carbon fiber tubes, aluminum lugs, and aluminum fork. It was considered the first affordable carbon-fiber road bike.
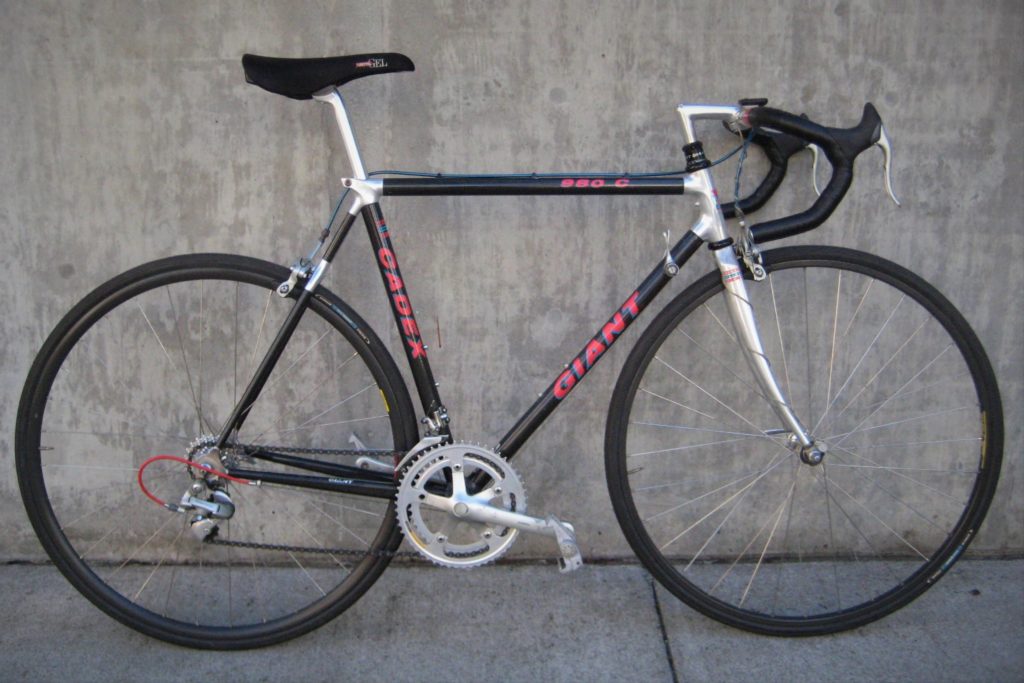